I/P Transducers: Bridging Pneumatics and Electronics in Industrial Automation
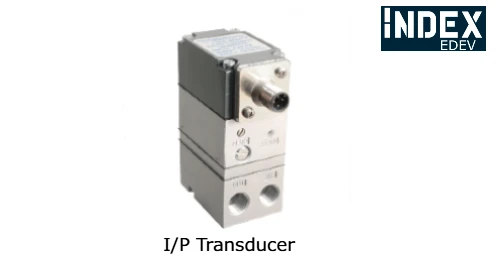
Overview
In industrial automation, achieving seamless communication between electronic and pneumatic systems is critical. I/P transducers, or Current-to-Pressure transducers, serve as the bridge between these two realms. They convert an electrical input signal (commonly a 4–20 mA current) into a proportional pneumatic output, enabling precise control over actuators, valves, and other pneumatic devices.
With advancements in automation and the increasing integration of smart systems, I/P transducers have become indispensable in industries such as oil and gas, chemical processing, and manufacturing. This article explores their working principles, key features, benefits, and applications, highlighting their importance in achieving efficiency and accuracy in process control.
How Does an I/P Transducer Work?
The operation of an I/P transducer involves three primary stages: signal conversion, pressure generation, and feedback control. Below is a detailed explanation of how these stages work:
- Electrical Signal Input:
The transducer receives an electrical signal, typically a current in the range of 4–20 mA, from a controller or other electronic device. - Conversion to Pressure Signal:
The input current is applied to an electromagnetic coil, creating a magnetic field that interacts with a diaphragm or flapper mechanism. This interaction generates a proportional pneumatic pressure output, which is sent to the connected pneumatic system. - Feedback Mechanism:
Most modern I/P transducers include a feedback loop that continuously monitors the output pressure. This ensures that the pneumatic signal accurately matches the input current, correcting any deviations in real time.
Key Features of I/P Transducers
- High Accuracy and Repeatability:
I/P transducers provide precise signal conversion, ensuring accurate control over pneumatic devices. Their repeatability ensures consistent performance over time. - Compact and Robust Design:
These devices are typically compact and designed to withstand harsh industrial environments, including exposure to temperature fluctuations, vibrations, and corrosive substances. - Wide Signal Range:
I/P transducers accommodate a broad range of electrical inputs and pneumatic outputs, making them versatile for various applications. - Fail-Safe Operation:
Many transducers are equipped with fail-safe mechanisms to maintain system stability in case of input signal loss or other malfunctions. - Low Air Consumption:
Modern transducers are designed for efficient operation, consuming minimal compressed air while delivering precise outputs.
Types of I/P Transducers
I/P transducers are available in several configurations to meet specific industrial needs:
- Direct-Acting I/P Transducers:
These transducers convert the electrical input directly into a proportional pneumatic output without additional amplification, suitable for low-pressure applications. - Force-Balance I/P Transducers:
Using a feedback mechanism, these transducers maintain precise pressure output by balancing the forces acting on the diaphragm. They are ideal for high-accuracy applications. - Explosion-Proof I/P Transducers:
Designed for hazardous environments, these transducers are built to operate safely in areas with flammable gases or vapors. - Smart I/P Transducers:
Equipped with digital communication protocols such as HART, these transducers allow remote calibration, diagnostics, and monitoring, making them compatible with Industry 4.0 systems.
Advantages of I/P Transducers
- Seamless Integration:
I/P transducers enable smooth communication between electronic controllers and pneumatic systems, simplifying process automation. - Enhanced Process Control:
The precise conversion of electrical signals to pneumatic outputs ensures accurate control over actuators, valves, and other devices, improving system performance. - Energy Efficiency:
By consuming minimal compressed air and electrical power, I/P transducers contribute to energy savings in industrial processes. - Reliability in Harsh Environments:
Designed to withstand challenging conditions, I/P transducers deliver consistent performance even in extreme temperatures, high humidity, and dusty or corrosive atmospheres. - Low Maintenance Requirements:
With fewer moving parts and robust construction, I/P transducers require minimal maintenance, reducing downtime and operational costs.
Common Applications of I/P Transducers
I/P transducers find applications across a wide range of industries:
- Oil and Gas:
Used in the control of pneumatic valves and actuators for flow regulation, pressure control, and safety systems. - Chemical Processing:
Enable precise control of reactant flows and temperatures by interfacing with control valves and dampers. - Power Generation:
Help regulate boiler controls, turbine systems, and other critical processes in power plants. - Food and Beverage Industry:
Ensure accurate control of pneumatic systems in bottling, packaging, and processing operations. - HVAC Systems:
Used in the control of dampers, fans, and other pneumatic devices to regulate airflow and maintain environmental conditions. - Pharmaceuticals:
Provide precise control in processes like blending, mixing, and pressure regulation in sterile environments.
Maintenance Tips for I/P Transducers
To ensure the reliable operation of I/P transducers, regular maintenance is essential. Here are some tips:
- Inspect for Contamination:
Clean the pneumatic and electrical connections regularly to prevent contamination or blockages that can affect performance. - Check Calibration:
Periodically verify and adjust the calibration to maintain accuracy. Many modern transducers include self-calibration features. - Monitor Air Supply Quality:
Ensure that the compressed air used is free from moisture, oil, and particulates, as these can damage the transducer. - Test the Feedback Loop:
Check the feedback mechanism to ensure that the output pressure matches the input signal consistently. - Replace Worn Parts:
Inspect seals, diaphragms, and other components for wear and replace them as needed to prevent system failure.
Future Trends in I/P Transducer Technology
As industrial automation evolves, I/P transducers are becoming more advanced to meet the demands of modern systems. Key trends include:
- IoT and Smart Features:
Integration with IoT platforms enables remote monitoring, diagnostics, and predictive maintenance, reducing downtime and enhancing efficiency. - Improved Energy Efficiency:
Innovations in design and materials are reducing energy consumption, making I/P transducers more sustainable and cost-effective. - Miniaturization:
Compact designs are being developed to fit into smaller systems, expanding the range of applications for I/P transducers. - Enhanced Safety Standards:
New designs focus on improving explosion-proof and fail-safe features to meet stricter safety regulations in hazardous environments.
Conclusion
I/P transducers are a critical component in industrial automation, offering a reliable means of converting electrical signals to pneumatic outputs. Their versatility, precision, and durability make them essential in industries ranging from oil and gas to pharmaceuticals. By understanding their working principles, advantages, and applications, businesses can leverage I/P transducers to optimize their processes, improve efficiency, and reduce costs.
As technology advances, the role of I/P transducers in smart automation and Industry 4.0 will continue to grow, further enhancing their value in modern industrial systems.