Top Quality Management Tools: Descriptions, Use Cases, and Benefits
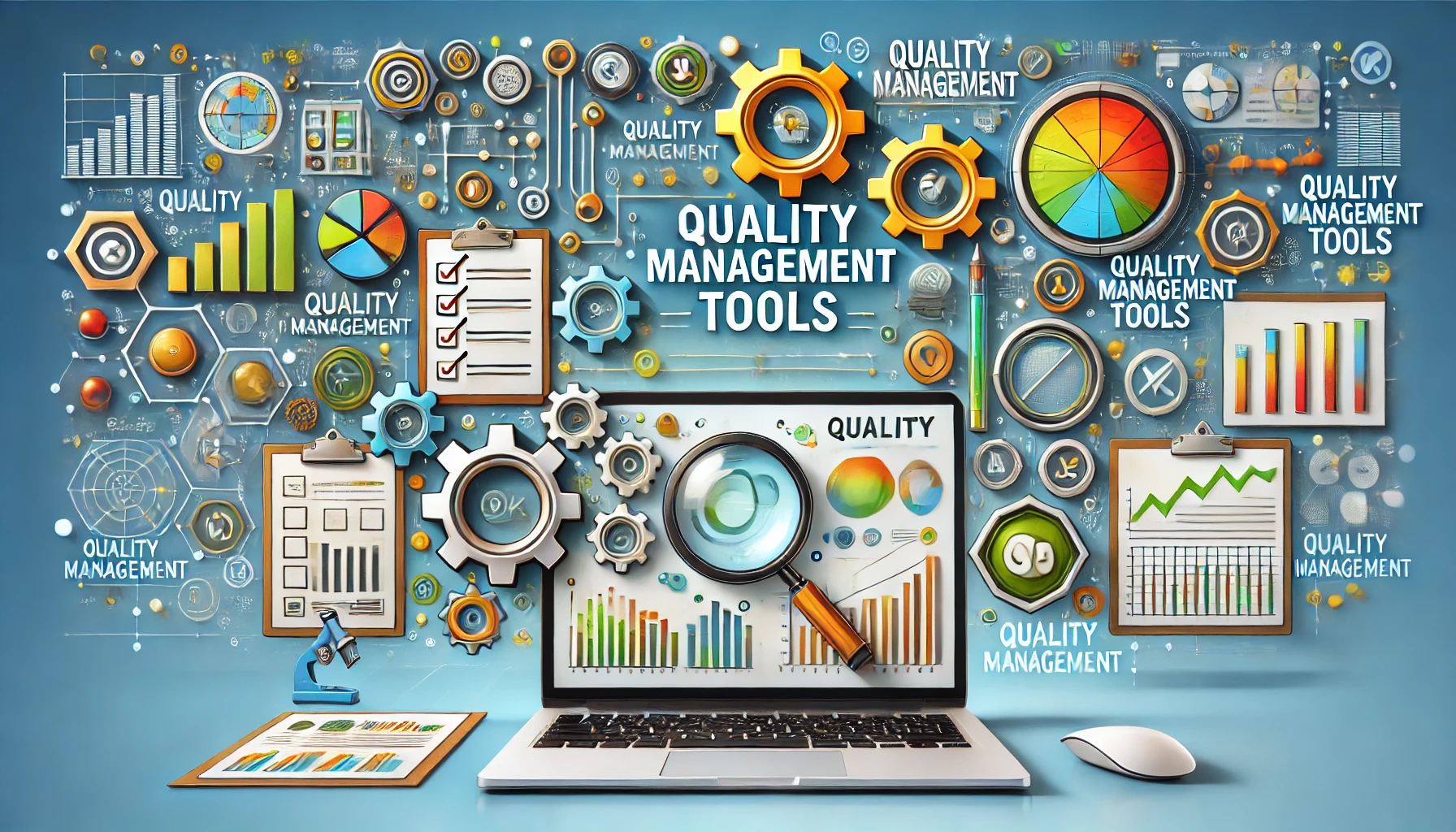
Overview
Quality management tools are critical for organizations striving to improve processes, reduce waste, and enhance overall efficiency. These tools offer structured methodologies to identify problems, implement solutions, and ensure long-term success. Here’s an overview of the most widely used quality management tools, their descriptions, use cases, effectiveness, and ease of use.
1. Plan-Do-Check-Act (PDCA) Cycle
Description:
The PDCA Cycle is a continuous improvement process used to test, monitor, and refine processes iteratively.
Use Case:
- Process improvement.
- Problem-solving.
- Iterative learning.
Effectiveness:
Highly effective for continuous improvement in both small and large-scale processes across industries.
Ease of Use:
Easy to implement and flexible for various industries.
2. Six Sigma
Description:
Six Sigma is a data-driven methodology designed to reduce defects and improve quality.
Use Case:
- Used in manufacturing, healthcare, and service industries to reduce defects.
Effectiveness:
Highly effective for defect reduction, especially in process-heavy environments.
Ease of Use:
Can be complex and often requires training (e.g., Green Belt, Black Belt certifications).
3. Lean
Description:
Lean focuses on eliminating waste (non-value-added activities) in processes.
Use Case:
- Mainly applied in manufacturing and service industries to improve efficiency.
Effectiveness:
Effective in eliminating waste and streamlining processes, which increases efficiency and value.
Ease of Use:
Easy to understand but requires a cultural shift and organizational commitment.
4. DMAIC
Description:
DMAIC is a structured problem-solving methodology comprising five stages: Define, Measure, Analyze, Improve, and Control.
Use Case:
- Primarily used for process improvement within Six Sigma projects.
Effectiveness:
Very effective for deep, data-driven analysis and process optimization.
Ease of Use:
Requires training and expertise, often used in conjunction with Six Sigma.
5. Root Cause Analysis (RCA)
Description:
RCA is a problem-solving method that identifies the root cause of issues.
Use Case:
- Used to diagnose problems and prevent recurrence in operations and products.
Effectiveness:
Highly effective in identifying underlying problems and preventing future issues.
Ease of Use:
Relatively easy to use, especially with tools like the Fishbone Diagram.
6. Fishbone Diagram (Ishikawa)
Description:
A visual tool for identifying potential causes of a problem.
Use Case:
- Helps in identifying root causes of quality problems in manufacturing, healthcare, etc.
Effectiveness:
Effective for brainstorming and identifying multiple causes of a problem.
Ease of Use:
Easy to use and very visual, suitable for team collaboration.
7. Total Quality Management (TQM)
Description:
TQM is a management approach focused on achieving long-term success through customer satisfaction.
Use Case:
- Used across organizations to involve all employees in improving processes and products.
Effectiveness:
Effective in fostering a quality culture and engaging employees in quality improvement.
Ease of Use:
Requires commitment and long-term involvement from all staff.
8. Failure Mode and Effects Analysis (FMEA)
Description:
FMEA is a systematic method for evaluating potential failures in a product or process.
Use Case:
- Primarily used in product development and design processes to anticipate failures.
Effectiveness:
Very effective for identifying risks and failures before they occur, especially in product design.
Ease of Use:
Requires detailed knowledge and data; may be time-consuming.
9. Balanced Scorecard
Description:
A strategy performance management tool that tracks key performance indicators (KPIs).
Use Case:
- Used by organizations to measure performance beyond just financial metrics.
Effectiveness:
Effective in aligning operational activities to strategic goals and enhancing overall business health.
Ease of Use:
Easy to implement with clear metrics but requires strategic alignment.
10. Kaizen (Continuous Improvement)
Description:
Kaizen is a philosophy focused on incremental, continuous improvement in processes.
Use Case:
- Applicable to any area of an organization for gradual, ongoing improvements.
Effectiveness:
Effective for driving small, continuous changes that cumulatively lead to significant results.
Ease of Use:
Easy to implement, but requires a mindset shift for organizational buy-in.
Conclusion
Selecting the right quality management tool depends on your organization’s goals, industry, and specific challenges. Whether you’re aiming to reduce defects with Six Sigma, foster a culture of improvement with Kaizen, or identify risks with FMEA, these tools can significantly enhance your operational efficiency and quality standards. By integrating these methodologies, organizations can achieve sustained growth and customer satisfaction.