Understanding Constant-Pressure Modulating Valves: A Key Component for Optimizing Fluid Control Systems
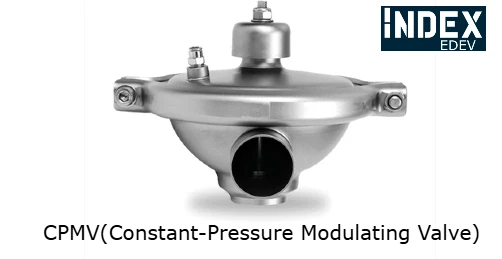
Overview
In many fluid control systems, maintaining a constant pressure is essential for system stability, efficiency, and safety. Constant-pressure modulating valves (CPMVs) are designed to achieve just that—keeping pressure at a stable level despite variations in flow rate, load changes, or system conditions. CPMVs are widely used across industries including HVAC, water treatment, industrial automation, and refrigeration, offering precise control and responsiveness to dynamic demands. This article explores the inner workings, applications, benefits, and considerations for CPMVs, giving you a full understanding of their role in fluid control.
What is a Constant-Pressure Modulating Valve?
A constant-pressure modulating valve is a control valve designed to automatically regulate and maintain a constant downstream pressure, regardless of fluctuations in flow rate or upstream pressure. By maintaining this steady pressure, CPMVs prevent pressure surges, protect equipment, and ensure smooth operation across a wide range of applications. They operate by sensing the downstream pressure and modulating their opening to maintain a set pressure, reacting dynamically to changes in demand or system load.
How Constant-Pressure Modulating Valves Work
The primary function of a constant-pressure modulating valve is to control the flow rate in a system to keep the downstream pressure at a specific level. Here’s a simplified breakdown of how they work:
- Pressure Sensing Mechanism:
CPMVs are equipped with a pressure sensor or diaphragm that detects the downstream pressure. As this pressure fluctuates, the sensor detects these changes and sends a signal to the valve actuator. - Automatic Modulation:
Based on the sensed pressure, the actuator adjusts the valve opening to increase or decrease flow. If the downstream pressure falls below the set level, the valve opens wider to allow more fluid to flow. Conversely, if the downstream pressure rises above the setpoint, the valve closes to restrict flow. - Feedback Control Loop:
Most CPMVs operate within a closed-loop control system. This loop allows the valve to continually adjust based on real-time pressure data, ensuring a constant downstream pressure even as operating conditions vary.
Types of Constant-Pressure Modulating Valves
Constant-pressure modulating valves come in various designs to suit different applications and fluid types. The most common types include:
- Pilot-Operated Valves:
These valves use a pilot mechanism to sense pressure and adjust the main valve accordingly. The pilot mechanism modulates the main valve to keep the downstream pressure steady, offering high accuracy and responsiveness. Pilot-operated CPMVs are widely used in industrial and commercial applications for their stability and reliability. - Direct-Acting Valves:
Direct-acting valves operate based on the downstream pressure pushing directly against a diaphragm or spring. As pressure rises or falls, the valve opens or closes to maintain the set pressure. These valves are simpler in design and are commonly used for lower-pressure systems or applications where fine adjustments are not required. - Electrically Actuated Valves:
In electrically actuated CPMVs, an electric actuator controls the valve opening based on pressure sensor data. These valves are often used in automated systems where they can be integrated with digital control systems, providing greater precision and control. - Hydraulically Actuated Valves:
These valves are commonly used in high-pressure systems. A hydraulic actuator responds to pressure signals to modulate the valve, ensuring steady pressure in applications such as heavy machinery or oil and gas pipelines.
Key Benefits of Constant-Pressure Modulating Valves
Constant-pressure modulating valves provide several benefits across a wide range of applications:
- Stable System Pressure:
By maintaining a consistent downstream pressure, CPMVs help stabilize the entire system, preventing pressure spikes that could damage equipment or cause leaks. - Energy Efficiency:
CPMVs optimize fluid flow to prevent overuse of pumps and compressors, resulting in reduced energy consumption and lower operational costs. - Reduced Wear and Tear:
Constant-pressure modulation minimizes the cycling of pumps, compressors, and other equipment, leading to less mechanical wear, longer component lifespans, and reduced maintenance requirements. - Enhanced Safety:
By controlling pressure within safe limits, CPMVs reduce the risk of over-pressurization, which can lead to ruptures or hazardous leaks. - Improved Process Control:
Many industrial processes rely on precise pressure control for product quality. CPMVs enable such processes by providing accurate, real-time control over fluid pressure.
Common Applications of Constant-Pressure Modulating Valves
The versatility of constant-pressure modulating valves makes them ideal for various industries and applications:
- HVAC Systems:
In heating, ventilation, and air conditioning systems, CPMVs regulate refrigerant or water flow, maintaining optimal pressure for efficient heat transfer and balanced temperature control. They help reduce energy use and prolong system life in both residential and commercial buildings. - Water Distribution and Treatment:
Water supply and treatment facilities use CPMVs to maintain consistent pressure in water distribution lines, ensuring steady flow to homes, businesses, and industrial facilities. They are also used in wastewater treatment processes to control chemical dosages and flow rates accurately. - Industrial Process Control:
Many manufacturing and processing industries, including pharmaceuticals, chemicals, and food and beverage, require precise pressure control for product quality and consistency. CPMVs provide the necessary regulation in processes such as mixing, filling, and packaging. - Refrigeration and Cooling Systems:
Constant-pressure modulating valves are essential in refrigeration systems, where they regulate refrigerant flow to maintain stable temperatures. This is crucial in industries like food storage and pharmaceuticals, where precise cooling is essential. - Hydraulic and Pneumatic Systems:
In systems that rely on hydraulics or pneumatics, CPMVs are used to maintain steady pressure, improving equipment efficiency and reducing the likelihood of mechanical failures.
Choosing the Right Constant-Pressure Modulating Valve
Selecting the appropriate constant-pressure modulating valve depends on the specific requirements of your application. Key factors to consider include:
- Pressure Range:
Ensure the valve can operate within the desired pressure range for your application. Over-pressurization can damage the valve, while under-pressurization may result in insufficient flow control. - Flow Rate Requirements:
Determine the expected flow rate and choose a valve that can handle these conditions. Flow rates too high for the valve may cause inaccuracies or damage. - Fluid Type:
The type of fluid (gas or liquid) and its properties, such as viscosity and corrosiveness, will influence valve selection. Some CPMVs are specially designed for use with certain fluids and may have coatings or materials that resist corrosion or wear. - Response Time and Control Sensitivity:
Consider whether the application requires rapid response times or fine control adjustments. Applications with rapid demand fluctuations may benefit from pilot-operated or electrically actuated valves that can respond quickly. - Material Compatibility:
Select a valve made from materials compatible with the fluid to avoid corrosion and ensure durability. Stainless steel, brass, and certain plastics are commonly used in CPMVs based on their corrosion resistance and strength.
Future Trends in Constant-Pressure Modulating Valve Technology
As industries adopt more automated and connected systems, constant-pressure modulating valves are also evolving. Some emerging trends in CPMV technology include:
- Smart Valves with IoT Integration:
Smart CPMVs equipped with IoT capabilities allow for remote monitoring and data-driven maintenance. By gathering real-time pressure data, these valves can alert operators to potential issues before they cause downtime. - Improved Actuation Mechanisms:
Advances in electric and hydraulic actuators are enabling finer control and quicker response times, particularly in high-pressure applications such as industrial and energy sectors. - Energy-Efficient Designs:
New CPMV designs focus on reducing energy consumption, making them suitable for green building systems and other sustainability-oriented applications. - Advanced Materials for Corrosive Environments:
With the demand for CPMVs in harsh environments, such as chemical processing or marine industries, manufacturers are developing valves made from advanced corrosion-resistant materials that offer longer life and greater durability.
Conclusion
Constant-pressure modulating valves are indispensable components for achieving stable, efficient, and safe operation in fluid control systems. From HVAC and water treatment to industrial process control and refrigeration, these valves ensure that downstream pressure remains steady regardless of changing flow rates or load demands. By understanding the types, benefits, applications, and considerations for CPMVs, professionals can select the right valve for their specific needs, leading to better system performance, reduced costs, and enhanced safety.
As technologies evolve, CPMVs continue to advance with IoT connectivity, smart capabilities, and innovative materials, offering even more possibilities for precise fluid control across industries. Whether you're designing a new system or optimizing an existing one, CPMVs offer the reliable pressure regulation that is crucial for today's complex applications.