Water Ring Compressors: Principles, Benefits, and Industrial Applications
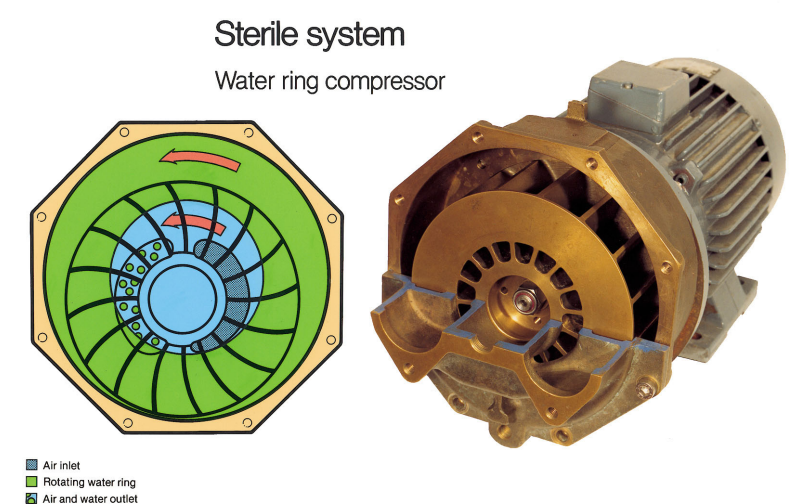
Overview
Water ring compressors, also known as liquid ring compressors, are a type of positive displacement compressor that uses water (or another compatible liquid) as a sealant. Their unique design allows them to effectively compress gases and create vacuums without generating significant heat, making them highly efficient and reliable for various industrial applications. Commonly used in chemical processing, food and beverage production, and pharmaceuticals, water ring compressors are valued for their durability, low maintenance requirements, and ability to handle both dry and saturated gases.
In this article, we will explore how water ring compressors work, their advantages, types, and typical applications, along with maintenance tips to ensure optimal performance.
How Does a Water Ring Compressor Work?
A water ring compressor uses a liquid ring created by a rotating impeller to compress gas within the chamber. Here’s a step-by-step breakdown of the process:
- Liquid Inlet and Impeller Rotation:
The compressor consists of a cylindrical casing with an impeller inside. Water (or another sealant) is introduced into the casing, filling a portion of it. When the impeller rotates, centrifugal force pushes the liquid outward, forming a ring along the inner walls of the casing. - Gas Compression Chambers:
As the impeller rotates, the gas enters through an inlet port into chambers between the impeller blades and the liquid ring. The eccentric positioning of the impeller within the casing causes these chambers to expand and contract as the impeller turns. - Compression and Discharge:
When the chamber contracts, the gas is compressed against the liquid ring. Once the gas reaches the desired pressure, it is expelled through the discharge port. This process is continuous, with gas entering, being compressed, and discharging with each rotation. - Liquid as a Sealant and Cooling Medium:
The water or liquid ring serves both as a sealant, preventing gas leaks, and as a cooling medium, absorbing the heat generated during compression. This keeps the compressor running cool and allows it to handle gas types that may be sensitive to temperature fluctuations.
Types of Water Ring Compressors
Water ring compressors are categorized based on their design and application requirements. Here are some common types:
- Single-Stage Water Ring Compressors:
Single-stage compressors are designed for low-to-moderate compression ratios. They are commonly used in applications that do not require high pressures, such as vacuum generation or low-pressure gas compression. - Two-Stage Water Ring Compressors:
Two-stage compressors are suitable for higher compression ratios and applications requiring greater vacuum levels. In two-stage designs, the gas undergoes compression in two separate stages, achieving a higher pressure than single-stage units. - Closed-Loop Water Ring Compressors:
In closed-loop compressors, the sealing liquid is recirculated within a closed system. This type is ideal for applications where contaminants in the gas could interfere with the process or where water conservation is a priority. - Open-Loop Water Ring Compressors:
Open-loop compressors use fresh water or liquid as the sealing medium for each cycle. This design is beneficial in applications where clean, uncontaminated gas output is required.
Advantages of Water Ring Compressors
Water ring compressors offer several benefits that make them suitable for demanding industrial applications:
- Low Operational Temperature:
Since water or liquid is used to cool the gas during compression, water ring compressors operate at lower temperatures than traditional air compressors. This feature allows them to handle temperature-sensitive gases effectively. - Reliable and Durable Design:
Water ring compressors have fewer moving parts compared to other compressor types, which minimizes wear and tear. The water ring acts as a cushion, reducing metal-to-metal contact and extending the lifespan of the compressor. - Ability to Handle Wet and Dirty Gases:
The water seal provides a barrier that can handle gases containing moisture, dust, or contaminants, making water ring compressors ideal for challenging environments. - Low Maintenance Requirements:
These compressors are generally easy to maintain, requiring periodic liquid replacement and minor adjustments. With fewer parts to maintain, they are cost-effective in the long run. - Consistent Vacuum Creation:
Water ring compressors are excellent at generating stable vacuums, which are useful in a wide range of industrial applications, such as vacuum packaging and gas extraction.
Common Applications of Water Ring Compressors
The versatility and reliability of water ring compressors make them valuable in multiple industries:
- Chemical and Petrochemical Industries:
In chemical processing, water ring compressors are used to handle gas mixtures that may contain corrosive or reactive components. They are also used for vapor recovery, solvent extraction, and in the processing of volatile organic compounds. - Food and Beverage Processing:
Water ring compressors are commonly used in vacuum packaging, bottling, and other processes where clean gas handling is essential. Their ability to generate a stable vacuum without overheating makes them suitable for delicate processes in food production. - Pharmaceutical Manufacturing:
In pharmaceutical applications, water ring compressors are used for vacuum distillation, filtration, and other processes that require a controlled environment with a low risk of contamination. - Pulp and Paper Industry:
The pulp and paper industry relies on water ring compressors for dewatering, gas recovery, and vacuum creation. Their ability to handle wet, fibrous materials makes them ideal for these processes. - Mining and Metal Processing:
In mining and metal refining, water ring compressors are used for gas recovery, extraction, and environmental control. Their durability allows them to withstand the harsh conditions often found in these industries. - Environmental Applications:
Water ring compressors are used for biogas compression, landfill gas recovery, and in environmental remediation processes where contaminated gases need to be compressed and controlled.
Maintenance Tips for Water Ring Compressors
Proper maintenance ensures that water ring compressors operate efficiently and have a longer lifespan. Here are some key maintenance tips:
- Regular Inspection of the Liquid Seal:
The water or sealing liquid should be monitored and replaced as needed. The quality of the liquid affects the compressor’s efficiency, so ensure it’s free of contaminants. - Check for Leaks:
Inspect the compressor casing and connections for leaks. Any loss of liquid could lead to reduced efficiency and potential overheating. - Monitor Temperature and Pressure Levels:
Keep an eye on operating temperatures and pressures to ensure the compressor is functioning within its specified range. Abnormal readings could indicate a problem with the impeller or a need for liquid replacement. - Clean Impeller and Internal Components:
Over time, buildup can occur on the impeller and internal surfaces. Periodically clean these parts to ensure smooth operation. - Lubricate Bearings and Moving Parts:
Although water ring compressors have fewer moving parts than other compressors, it’s important to keep bearings and other moving parts lubricated to prevent excessive wear. - Perform Routine Testing:
Regular performance testing, including pressure and vacuum level checks, can help identify potential issues before they lead to breakdowns.
Choosing the Right Water Ring Compressor for Your Application
When selecting a water ring compressor, consider the following factors:
- Required Pressure and Vacuum Levels:
Choose a single-stage or two-stage model based on your pressure or vacuum requirements. Two-stage compressors are ideal for higher pressures or deeper vacuums. - Sealing Liquid Compatibility:
Ensure the sealing liquid is compatible with the gas you intend to compress. In applications with aggressive gases, other sealants like oils or compatible liquids may be required. - Flow Rate and Capacity Requirements:
Determine the flow rate and capacity needed for your application to select a compressor that meets these specifications. - Environmental and Operational Conditions:
Consider environmental factors such as temperature and humidity, as these can impact the performance and lifespan of the compressor. In humid or contaminated environments, water ring compressors generally perform well due to their ability to handle moisture and particulates.
Future Trends in Water Ring Compressor Technology
Water ring compressors continue to evolve with advances in materials, efficiency, and IoT integration. Some notable trends include:
- Energy-Efficient Designs:
New designs focus on reducing energy consumption, improving sealant flow, and optimizing impeller performance to lower operating costs. - Smart Monitoring and IoT Integration:
IoT-enabled water ring compressors allow for real-time monitoring, predictive maintenance, and remote troubleshooting, making them suitable for Industry 4.0 applications. - Eco-Friendly and Water-Saving Options:
Closed-loop systems and advanced sealing methods are being developed to reduce water usage, which is beneficial for applications where water conservation is essential.
Conclusion
Water ring compressors are versatile, reliable, and highly efficient machines for compressing gases and creating vacuums in a wide range of industrial applications. Their ability to handle wet and dirty gases, low operating temperatures, and durability make them indispensable in sectors like chemical processing, pharmaceuticals, and food production. By understanding the design, advantages, and maintenance needs of water ring compressors, businesses can make informed decisions to optimize their processes and extend the compressor's lifespan.
Whether you need a single-stage compressor for a basic application or a two-stage, closed-loop system for more complex needs, water ring compressors offer a solution that balances performance with cost-effectiveness. As technology continues to advance, these compressors are likely to become even more efficient and capable, supporting industries in achieving their operational and environmental goals.